Dr Sukamal Deb, Lead, Anant Centre for Documentation and Design of Crafts (ACDC), Anant National University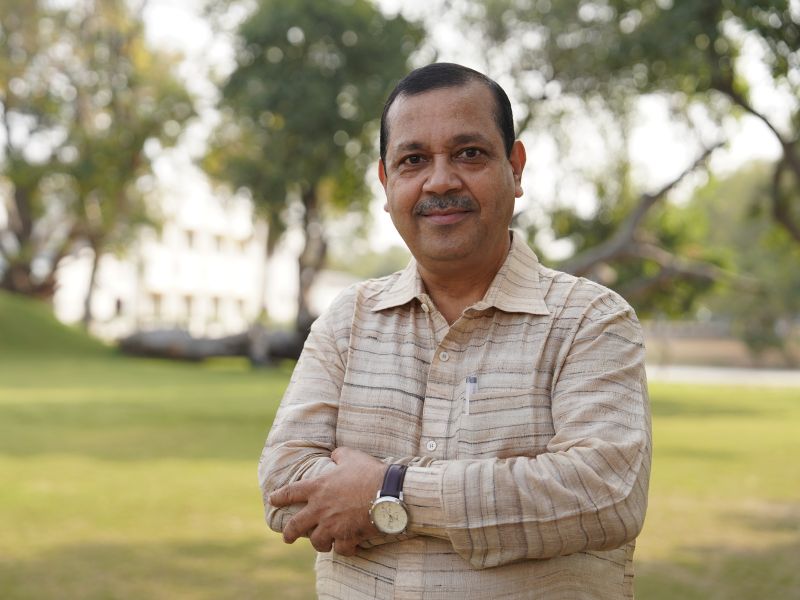
In one of the coolest dawns of 2024 on Jan 10, I got down at Badarpur rail junction from Dibrugarh Agartala Express with a mission to meet the Paatikar (Cool mat artisans) of Barak Valley, Assam. My destination was Ratanpur, Rahimpur, Baleswar and more villages under Kaliganj area.
I reached Chargola by road, recalling the famous Chargola exodus in 1921, one of the earliest organised labour movements of the country, had its origin in the Chargola valley tea belt of Karimganj sub-division at the southern fringe of the state of Assam, in the north east India. I am to walk down the bank of the Kachua Rivulet, bifurcated from Singla River that originates from Mizoram, to reach my destination, a cluster of artisans’ villages where Hindus and Muslims live for generations in brotherhoods of unparalleled cohesion. I read, on May 3, 2021 Badarpur College organised a seminar Revisiting Chargola Exodus in its centenary year 1921 – 2021, interestingly the exodus was initiated by an illiterate woman.
The Kaliganj area of Karimganj, a district in Barak Valley, its early history is hazy and obscure, once it had been famous for Shital Paati, the smooth and flexible mats made by plaiting an indigenous reed. Thousands of artisans, mostly women, were associated with this traditional cottage industry. The artisans are known as Paatikar belonging to Hindu and Muslim communities. Shital Paati literally means cool mat. The mat is thin, smooth and pliable, and made by plaiting an indigenous reed locally known as Murtha (Maranta Dichotoma), a locally grown lemon coloured reed with waxy leaves. It is a long-stemmed, knotless plant that grows abundantly in marshy areas. Sheetal Paati are traditionally made by men and women in a wide variety of patterns and sizes to supplement the income from agriculture, they are pliable and easy to fold and store, used as floor spread for sleeping and eating meals on and as prayer mats in shrines. They are popular in summers as mattresses as they are Sheetal or cool to the touch. The stem of Murtha is cut near the ground and skinned. The outer is made into strips of about 3 mm and wetted before interlacing and plaiting them in an oblique manner. To finish the mat, the cut ends are returned into the weave diagonally. Motifs are woven by changing the pattern of interlacement and introducing dyed reed strips. The size of the strip and density of the weave determine the pliability of the mat. The mats were originally made in Bangladesh and are now being made in the villages. This has a global recognition and market but languishing rapidly.
The Sheetal Paati weaving is one of the potential enterprises for sustainable livelihood generation. The study revealed that many farmers were engaged in this enterprise to improve their socioeconomic status. Prior to independence, Barak Valley was a part of Surma Valley when Sylhet and Cachar, two Bengali speaking districts of the Bengal Presidency, were separated and combined to form Assam in 1874, Surma Valley administrative division was created. Until Sylhet’s secession to East Pakistan in 1947 Cachar district remained a part of Surma Valley. After Sylhet, Cachar district became the lone Bengali stronghold in Assam. In the late twentieth century, Barak Valley became the name of Cachar district which included remnants of erstwhile Sylhet. Historically, Barak Valley has gone through partition twice, once in 1874 when it was severed from Bengal and again in 1947 when Sylhet voted to secede. In post-independent Assam, Barak Valley turned into an alien land. Subsequent actions of the leadership have significantly impacted the socio-political life and strengthened the sense of isolation of the Valley that struggled to preserve her identity despite going through a serious existential crisis, with multi-dimensional poverty level at around 46 percent, lower than Hailakandi, around 51 percent, another Barak Valley district, the sickness or to extreme demise of many crafts and fall of economy can’t be seen parted from this reality. We will not go further here unravelling the intricate socio-economic and political processes that derogated Karimganj district to one of the most backward district from the most important national and international centre of trade and commerce during pre-independent era when Sheetal Paati remained one of the supreme crafts of the Valley.
Sheetal Paati making involves a series of steps from plantation, weeding, stem cutting & peeling, boiling, colouring, weaving and finishing. Reeds are cultivated in March – April. Once the plants grow they usually survive for around 20 years, a mature stem with proper ensures good quality mat. Each stem of reed is split into several pieces and further into three slices outer, middle and inner. The outer part is used to make mota or thick Paati, the middle is woven into bokar Paati, and the inner part is split into strips for other uses not for Paati making. The split strips called betis are then weaved to make the mat. Betis are soaked in a mixture of hot water and rice starch for 3 to 4 days, thereafter the stuffs are boiled until they turn white in colour. These strips are dried in the sun. The method results in a better cooling effect, weaving starts from a corner and proceeds until the completion of the mat.
Shital Paati production is a household industry, where men traditionally collect reeds and prepare it for the mats, while the women weave them. It is a laborious process. The mat owes its name to the fact that it provides a cool surface to sit or sleep on. Hence, it is very popular in the hot and humid weather conditions of the North East, where it is mainly used in traditional households for sleeping or as prayer mats. The artisans of Shital Paati have no alternative source of income, their socio-economic conditions are miserable and most of them do not know any other trade except this. The literacy rate of the Paatikar community residing in the Kaliganj area is low 20 per cent. There is no high school in the area, and the State Government is yet to take any special step to uplift the community. Sheetal Paati has a wide variety of patterns and sizes easy to fold and store. This product had global recognition in the pre-independence era with a global market. But this is entering a dark oblivion, like many other languishing crafts of the North East. Off late, the Anant National University, Ahmedabad, India’s first design university, has embarked upon to document these languishing crafts. The university has opened Indian Designs and Innovative Crafts (INDIC) Centre dedicated to this inter alia.
UNESCO has recognised the traditional art of Sheetal Paati weaving of Sylhet, the neighbouring district of Karimganj in Bangladesh and included it in the Representative list of the Intangible Cultural Heritage of Humanity.
The Valley people believe that the existence of Sheetal Paati weaving traces its origin back to ancient times, used for sitting in meditation by the sages. These cool mats, a rural craft, evolved conventional uses. Technological advance may have brought alternate similar products but this is in no way reduces its importance, the utility or the craftsmanship.
The cooling function of these mats during summer is one of its unique properties. You look for something to beautify your space with a traditional vibe, these mats can be a good choice, and it’s an alternative traditional bedding. Its natural texture, excellent motifs and vibrant colours witnesses the creativity of village artisans. Quality is recognized through their smoothness, glossiness and texture. The more the smoothness or the finer the texture, the better quality. It is said the best kind are the ones that are so smooth that even a snake can’t glide over them. The colours used are not made of any chemical composition, the excellent beauty is achieved by using the organic extracts from the seeds of tamarind, leaves, hibiscus flowers, mango tree barks and other natural sources.
Village Ratanpur has 600 families with around 3000 population. They belong to OBC, Minority OBC and SC communities. Sheetal Paati craft is practiced by all these families, they cultivate Murtha, one bigha of marshy land (1338 sq. m.) produces Murtha of Rs.20000 with which one can make Sheetal paati worth Rs.34000. Sales take place on two weekly market days when all their products get all sold to the middlemen. Ismail Ahmed (44) a Sheetal paati artisan shared many interesting facts. Ismail’s family has 7 members 4 make Sheetal Paati earn Rs.9000 a month but the raw materials Murtha costs Rs.3000. Thus artisans together earn just Rs.6000, each less than Rs.2000 a month yet they cling to this profession for generations. When they were asked if they love this work, there were mixed responses, some said in absence of alternate livelihood it is their compulsion yet other said it’s their identity, putting me to ponder. Nazima (15) a class IX student while demonstrating her weaving skill said if she works regularly she can weave one mat in ten days, but she has to go to school walking miles, while staring at Ismail her father, she dreams to be a doctor. Ismail said there are only few in the village who did their BA, one works with Ajmal Foundation in Dubai. The next villages are Baleswar and Karimpur where all families practice this craft and tell similar stories.
My visit to Nandapur, a village of 200 families and 1000 population, 150 families are SC (Namasudra) community. They all work on Bamboo crafts, women are more hard working. Through this craft Shipra (38), class II, earns Rs.2000, Vishnu (42) and his wife Anjana (37) earn Rs.7000, Aparna (32), class II, earns Rs.3000, Shibu (51) and his wife Bappi (43) earn Rs.6000, Sandipa (31), class III, earns Rs.4000, Sandhya (33), earns Rs.4000 PM and Sankari (38), earns Rs.4000 a month. They make Tukri (round Basket), Runga (fishing apparatus) and bamboo mats. Similar is the story of Barbari, another nearby village. The entire Barak Valley was famous for bamboo crafts but are becoming languishing day by day. There is enough need to promote and innovate these traditional crafts. As I walked down from house to house I discovered there are no roads to reach their dwellings, if it would have been the rainy season, it would have been difficult to reach them. I dared how the school children move out in monsoon. The village has just one LP school, there is no post office, no bank. They have electricity while the water supply project is just made operational and hardly anyone is in Government jobs. The village Nathupur has 65 families, 270 population, all Hindu, belong to SC community, all are cane artisans. Sudip (45), class II, working for 15 years on round canes, his wife Swapna (Bhattacharjee), class XII is from Tripura. The couple work on a variety of cane species like Raidang (Golla), Lezai, Pani Lezai earning Rs.12000 to 13000 a month. Dipak (35), class X of nearby house is an entrepreneur, has set up a cane furniture making unit, giving employment to 45 village artisans. I couldn’t meet as he was in Guwahati participating in a craft exhibition there. He owns a pucca house, visibly has good financial status. Rupak, his brother, is studying in BA.
Next I reached Nasir Ali (70) at Jotai village, a family of 18 members, all females weaving Sheetal Paati. Sofia (30) weaves Sheetal paati for 15 years. They do it for generations, she weaves 4 Paati of size 7 x 5 sq. ft. a month each costs1700 which includes raw material of Rs.400 for each, Faruk (36) her husband, a dumb, splits Murtha with exceptional accuracy. The couple has 2 children, a boy and a girl. Khalida (25), class VII works on this craft since she married into this family. She, mother of 3 children is a brilliant weaver earns Rs.3000 pm from this. Her husband works in a shop. Nasir Ali’s one son is a truck driver, who earns little more.
NGO activist Subudh (42) extended help to facilitate the study. He, in a run-down bike hired from a neighbor, reached the Chargola Bridge over the Kachua where I disembarked from the car, to receive me. His family offered me rice and fish curry for lunch, was of great help.
There is an urgency to transform Rural India, the invisible suppressed hinterland. All our endeavours should be a powerful means towards this. We need to work towards powering income generation, facilitating the rise of positive energy and investing in innovation, all at the bottom of the pyramid for they live without abundant, affordable energy, there is no modern agriculture, no efficient transportation, no way of linking villages and cities, their crafts and indomitable skills are not known to larger world. For decades the strategy around their development, for the people living in poverty, has not replicated the change. Rural households and businesses have to unlock incredible growth, innovators and entrepreneurs like Deepak inspire us, we need to break down the barriers, we need to build decentralized, renewable infrastructure, facilitate the Nano and micro-enterprises. For these are the crafts once lost their identity is also lost. A few pictures of the visit writes many stories of struggles and inspirations.
Also read: Anant National University: Building a Diverse and inclusive workforce for the future